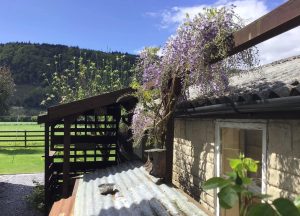
Once upon a time. There stood next to Mark’s abode a dusty cobweb ridden cast concrete garage. We can but assume the garage has been there for at least 30 years, most probably way longer. Never used as a garage and in its time a climbing wall and home recording studio. Let’s take a look at the process of how it went from zero to hero.
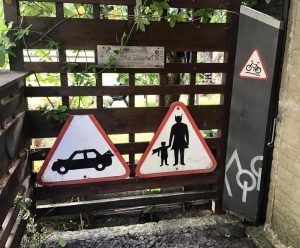
IN THE BEGINNING.
Imagine if you can… a garage built upon a concrete plinth. The garage walls are large sections of concrete panels fitted together by giant tongue and groove moulding and bolted. Each panel weighs approximately 60kg. There is no insulation, electricity or lighting. The roof is corrugated fibreboard or possibly asbestos! There are 3 small windows. On a good note it is sound and watertight. The site has only beautiful fields for neighbours.
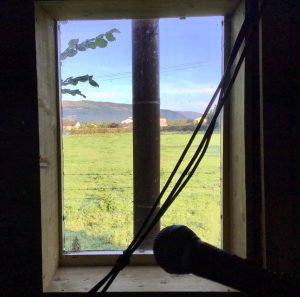
I guess before work commences one must have a vision of its use and an aspiration of what it should look like. Use – rehearsal room/social space. Aspiration – rustic Mississippi juke joint! Absolute musts are power, lights and warmth. The rest is just pleasing to the eye!
Here we go then. No frills explanation, this is what happened. A garage side was replaced by a modern locking door. The double garage doors were removed and replaced with a stud wall, the outside surface was plastered and painted. Every wall had a stud wall installed to it, all the cavities were insulated for warmth and soundproofing. A power supply was fed from the main property, basic lighting added and multiple wall sockets fitted at a height befitting amps, speakers and the like. The entire space including the ceiling was then plaster boarded and painted in plain white. The concrete floor was later sealed with floor paint. And this is how it remained for several years. Of course a token effort was made to tart it up, gig posters and minor decorations. But it remained pretty grim and pretty cold.
A BUILDING ON THE DELTA.
What do the old juke joints look like? Well of course they are all virtually built of wood and corrugated tin sheets. Everything within its walls should be pretty old school. The aim was to build every as cheaply as possible but at a tidy standard. There was no time limit and to this date there are still things to finish. But that is the nature of the build if money is tight. From the offset it was decided to baton the walls and overtime clad it with wooden panels. Pallet wood would be the cheapest and most obvious answer. However, in a rural area there is not an abundance of pallets and we would have needed hundreds of them. All requiring breaking down, de-nailing etc. The decision was made to go for rough cut 1″ planks, the width didn’t matter all sizes would be used. Indeed the varying widths would prove useful when filling all the blank spaces. Once cut to the required length the only other preparation was a quick sanding before screwing them to the pre placed batons. One solitary wall (behind the small stage/drum riser was clad in vertical corrugated tin. To date, there is a section of approximately one square metre to finish, timber prices are currently ridiculous. Above the windows is a length of rebar and each window has its own board panel that can be slid across to control the light.
In front of one window we put in a cheap log burner, a hole was drilled through the concrete wall for the flue. It’s now proper toasty! The HQ has a beer fridge which of course has been clad in wood, old brass coat hooks on the walls, a wire mesh notice board and a voodoo feature behind mesh on the far gable wall. Various points around the gaff have candle lanterns high on the walls. A couple of mirrors are recessed and some rustic shelves fitted to hold guitar pedals and niff naff. Amp leads, extension leads and instrument leads are hung by butcher’s hooks from the rebar. The only floor space taken is by an island on wheels made from scaffold boards and corrugated tin. This has the PA mixer on top and storage inside to keep the place tidy. Currently rugs adorn the floor.
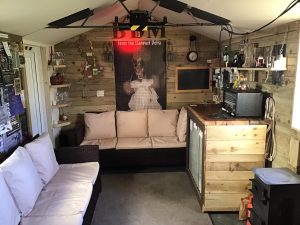
WHERE DO WE GO FROM HERE?
Work currently in process is to clad the ceiling with corrugated tin. Sourcing the tin is a problem, so far friends have come up trumps with a few sheets. We need about 8 more. Once the ceiling is clad a central rustic board will run the entire length and some old stage lighting installed. Other than that it’ll just be a case of keeping an eye out for decorative authentic decor. Maybe build a better drum riser? Maybe board the floor? Where do you stop?
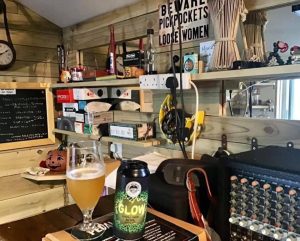
THE HQ’S USE
Obviously the weekly role is as the band rehearsal space. We’ve had pub nights and jolly ups and it’s regularly used to make video demos for the bands media. All in all once the fire is on the go, music playing and the lights down low this Delta juke joint is a joy to behold!
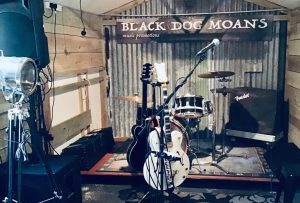